Model Predictive Control
demonstration for an EAF (meltdown) process model:
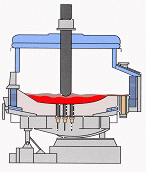 |
Warning: The results may not fit to your specific real furnace without some
parameter determination by inverse modelling.
This is mainly a demonstration of the MPC approach, i.e. mission critical
set values (arc power and DRI feeding) are determined by the model itself. |
Please select your parameters:
Example of the Results:
80t melt in a 100 MW furnace (30t scrap + 50t DRI, tapping at 1800 C):
The initial scrap mass
ms is
melted during the first 6 minutes. Thus the mean temperature of the solid material
TSolid increases, while the mean temperature of the liquid metal
TMelt decreases (possibly until
TMelt=Tliquidus).
This melting process can be seen by the increasing liquid steel mass
ml and the decreasing solid steel mass
ms.
As the model detects the end of the scrap melt down phase, DRI feeding is started.
The total mass in the furnace
m is thus increasing.
The DRI feeding rate
mDRI is calculated by the model in order to avoid icebergs and to
optmize tap-to-tap time for a given arc power PEL (100 MW).
As soon as the desired tapping mass of liquid steel is reached, the DRI feeding stops
and the melt is heated to the desired tapping temperature.

These results are thus obtained by calculating set values for the
arc power PEL and the DRI feeding rate
mDRI within the model:

Modelling assumptions:
coming soon